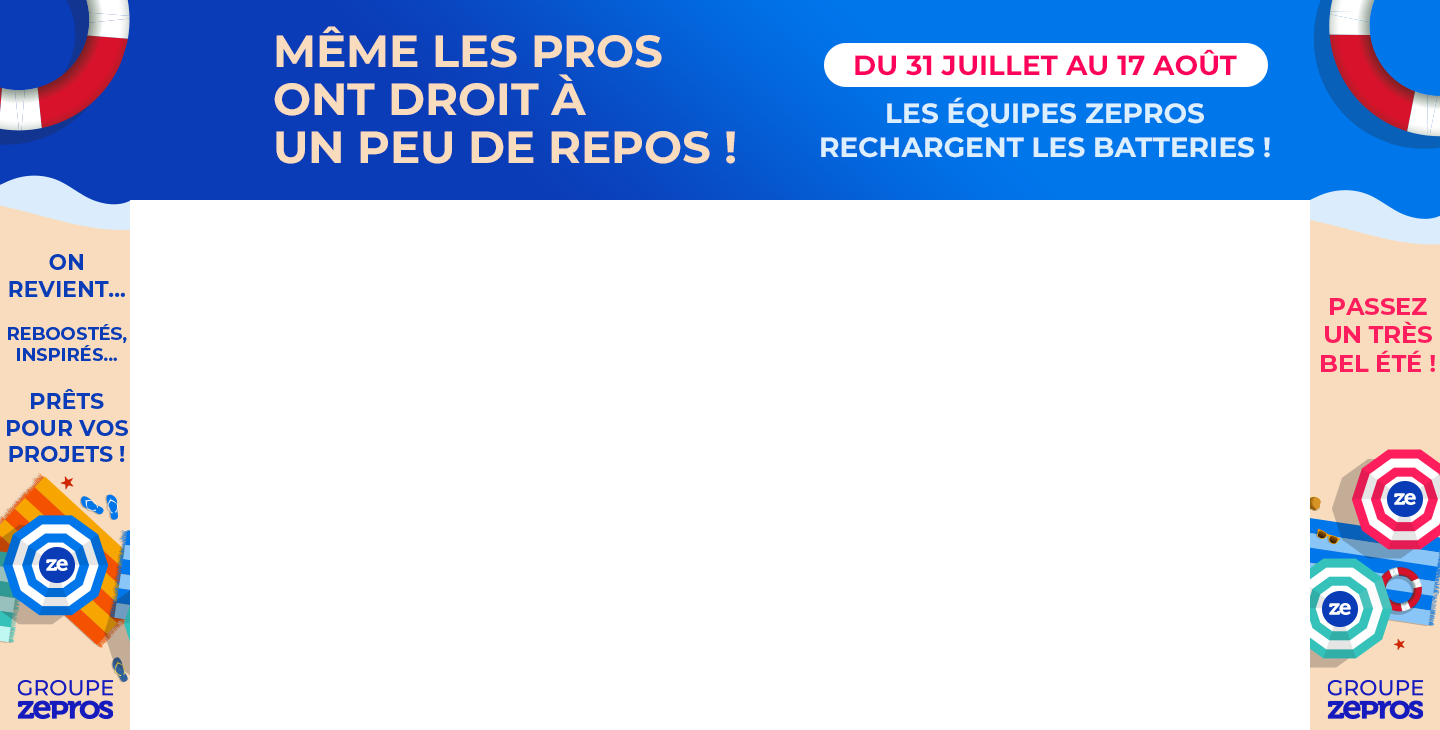
Churchill 1795, l'assiette anglaise
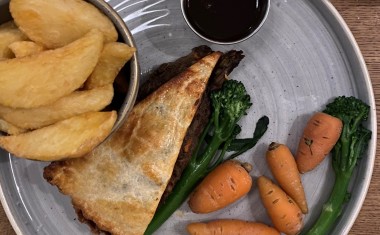
Au cœur de la campagne anglaise, perdue quelque part entre Manchester et Liverpool, une manufacture de vaisselle anglaise résiste à tout, mondialisation et Brexit compris. Churchill 1795 fabrique de la vaisselle pour les professionnels. D’une beauté et d’une résistance absolue. Reportage.
Pour y arriver depuis Paris, il faut prendre un avion direction Manchester, puis poursuivre en voiture, environ 40 min pour se perdre dans la campagne anglaise. Direction : Stoke-on-Trent, là où Churchill 1795 a sa manufacture, réunissant atelier de création, bureau de tendance et fabrication. Tout est fabriqué ici, et ce depuis 225 ans. La famille Roppert, qui a créé l’entreprise est encore propriétaire des lieux. « En 1984, nous avons changé de nom. Le nom de Winston Churchill était libre de droit. Churchill incarne le génie et la force britannique. Le nom était tout trouvé », explique Mary Jugnet, directrice commerciale de la marque en France.
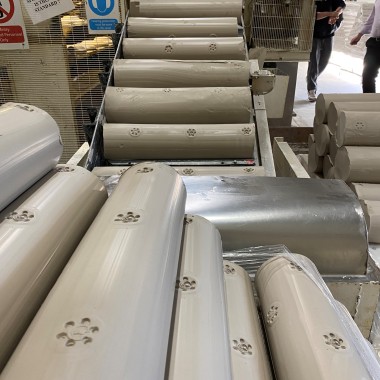
3 000 produits différents
Le design et l’innovation sont au cœur de la démarche de l’entreprise, qui s’adresse aux professionnels du CHR, tous types de restauration, y compris la street-food et la collective. Chaque année ce ne sont pas moins de 3 000 produits qui sont proposés dans 3 gammes différentes : Alchemy, Churchill et Art de Cuisine. Ce dernier est sourcé et fabriqué à l’étranger. Et des formes et des couleurs, il y en a : impossible de ne pas trouver son bonheur.
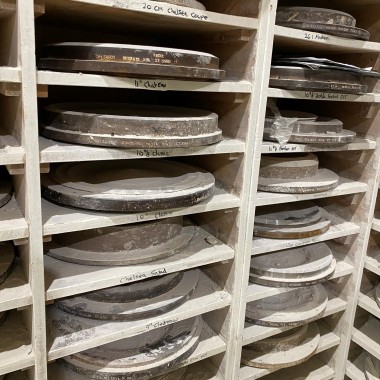
Fabrication maison
Nous prenons la direction de l’atelier de fabrication. C’est-à-dire : la porte d’à côté. L’argile, provenant de Cornouailles, sert à fabriquer la barbotine. Façonnée en gros boudins (photo 1) elle va ensuite être moulée et subir une première cuisine à 1 200 °C durant 48 h. Les pièces sont ensuite émaillées (photo). Les décors sont personnalisables. Tout est fait à la main. Plus de 570 employés travaillent ici.
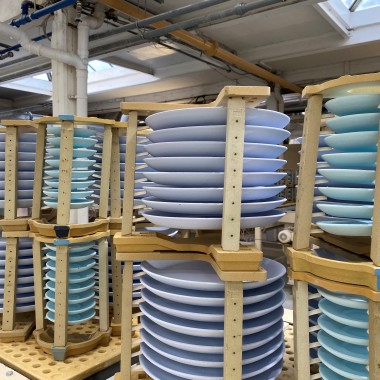

Travaux manuels
Une fois émaillées, les pièces sont mises sur des trépieds de séchage, manuellement (photo). Elles seront ensuite cuites à 2 reprises durant 7 h. Un polissage s’impose et lui aussi est manuel. C’est ce processus de fabrication qui donne sa robustesse aux pièces. Mark, le directeur de production prend une assiette et devant nous la fracasse contre une palette en bois (voir story sur Instagram), l’assiette ne cède pas, aucune fissure. 50 coloris sont disponibles (photo)
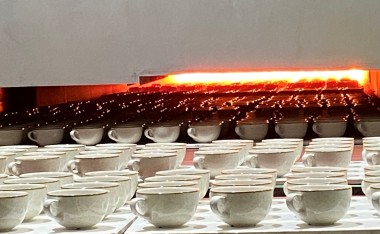
Cuisson à 1 200°C
Pour les tasses, le processus de fabrication dure 7 h en tout dont 5 h de cuisson (photo). Au bruit, les employés peuvent détecter si la pièce est fragile ou pas. Si elle l’est, elle est écartée.
Recyclage et panneaux solaires
Chaque pièce écartée est recyclée pour être réinjectée dans la production. L’entreprise a depuis quelques années investit plus de 20 M£ dans la modernisation de l’outil productif. Des panneaux solaires (4 500) ont été installés sur le toit pour apporter une autonomie énergétique (sauf les fours).
L’entreprise dispose de 4 entrepôts d’où elle expédie dans le monde entier. Pour l’Europe, il se situe à Rotterdam. Avec 7 millions de pièces en stock et 550 distributeurs dont 80 en France, elle répond à tous les besoins et toutes les envies
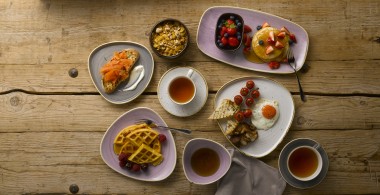
Sur le même sujet
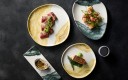
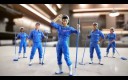
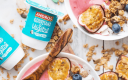
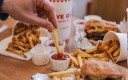